HI Guys,
I've been hammering on the VeeCU. Here is a trace of a normal engine start.
Since I don't have hardware yet, the bread board is programmed to accept rising edges of the top trace as the front secondary ignition inputs and the falling edges as rear cylinder secondary ignition input. It's just an easy way to get pulses 180 degrees out of phase with a single input.
So, ...
The yellow trace is/are the secondary ignition inputs which will be robbed from the secondary ignition coils.
The light blue trace is voltage to the secondary ignition coils. It replaces the inputs I stole :-)
The magenta trace is the output enable pin. While low the engine control IC outputs are enabled.
The dark blue trace is the injector pulses going to the right front cylinder.
For safety reasons, I don't allow any ignition or injector pulses until both the front and rear secondary ignition pulses have been seen during the most recent 10 seconds.
So the sequence goes like this:
The first falling edge of the top trace signals that the rear secondary ignition pulse was seen.
Then, when the rising edge is seen, both forward and rear have been seen withing 10 seconds and the outputs are enabled as seen on the magenta trace.
As soon as the outputs are enabled, since this is the first start since power up, a primer pulse is applied to all cylinders. This can be seen by the "wide" first pulse on the dark blue trace. This is a one time thing per power cycle unless the prime is manually rearmed.
On subsequent rising edges you can see the ignition pulses on the light blue trace. The pulses are initially in "impulse mode" behaving much like the secondary always has except the secondary has been retarded to 3 Deg. after TDC, hence like an impulse mag. As the engine passes from "Cranking" to "Starting" the ignition switches to Dwell control and pulls the ignition advance from the "Engine Tune". As the engine passes from "Starting to Running" the Dwell time is further reduced to 12 mSec as per Dyna Tec's advice.
So, it takes a minimum of three blades to fire the engine.
A lot of words for a simple pic :-)
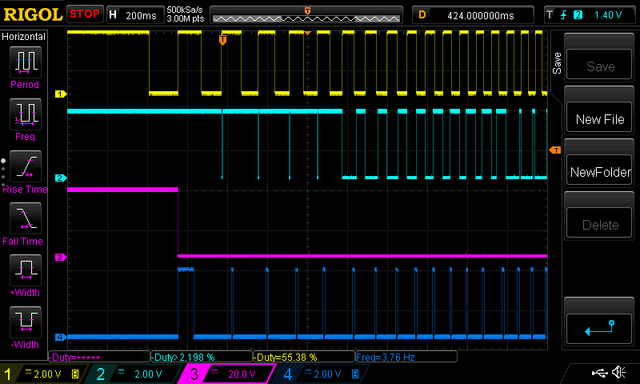
One more scope pic. This pic turns off all but the secondary ignition pulses and the injector pulses. During the early starting phase the pulses are "aimed" at the center of the down stroke. Since this is a "semi-sequential/staged sequential" system every other pulse hits an open intake valve. The other will hit half way down the power stroke. As the engine speeds up the injection pulses are timed to end just before TDC.
I implemented the reversionary mode and it works great on the bench. Right after engine start, a stability check begins. Once the engine is stable, the phase relation of the alternator pulses to the input secondary ignition pulses is calculated. If during engine run the secondary ignition pulses go away (for a heart stopping 1/2 sec), or has 10 percent missing pulses, the alternator takes over to drive ignition and injection. All of this is reported by the only means I currently have, winks and blinks of the panel LED.
I couldn't resist buying a copy of the enclosure for motivation. I like it. Every VeeCU electronic component is extended temp range. I intend to install the unit forward of the firewall. This enclosure is just about perfect for that purpose.
Just the right size. The right number of pins. Optional ferrites on all pins. Optional vent with "hydrophobic" membrane. Very tight/nice seal. Very affordable with sealed mating connectors.
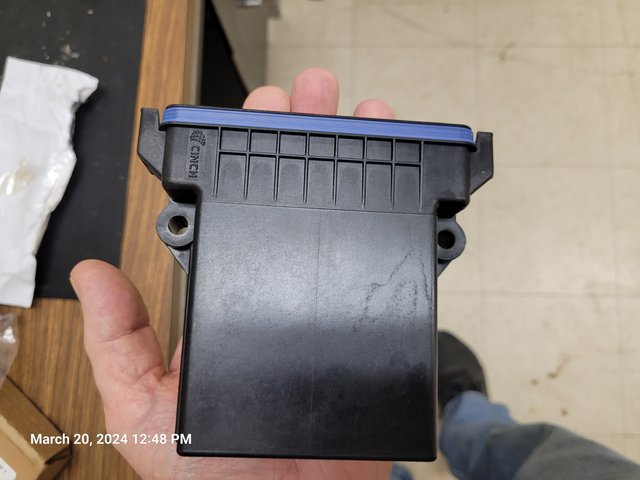
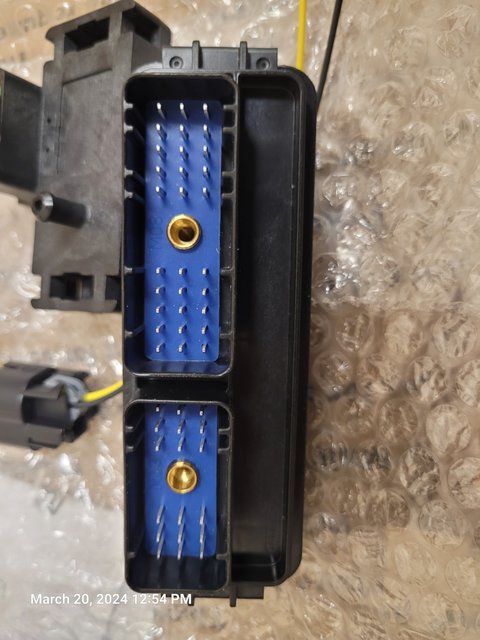
Anyway, if you can't tell, I'm get'n stoked. The user interface (i.e. switch reads and de-bounce, LED flash patterns etc. ...) is as far as I can go on the bread board. Software is just about ready to hook up to a real engine for "FMEA". It's gonna be fun :-) The schematic is complete and layout is under way.
The Design Engineer did this just to get an idea of how crowded, or not, the board will be. Not all components dragged on yet, most notably the IGBTs for ignitiion drive, but it's not going to be bad.
Forever Forward,
Wes